Supply Chain Agility: A Challenge or an Opportunity? (Part 1 of 3)
February 10, 2022 By: Louis J. Cerny | Topics: Supply Chain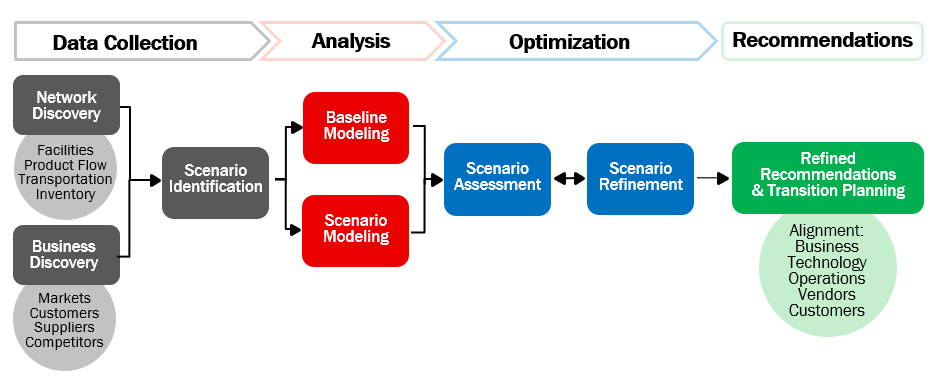
There is an old expression: “May you live in interesting times.” The origin is unclear, as some attribute it to a centuries-old Chinese curse. According to the website The Phrase Finder, it was from a 1939 communication from American politician Frederick R. Coudert to Austen Chamberlain, and later used by Robert Kennedy in a speech in South Africa.
Regardless of the origin, the expression definitely applies today, and I doubt there has ever been a more INTERESTING TIME for supply chain and logistics professionals. Having said that, I am confident that the profession is up to the task.
Finding workers is an ongoing challenge, and what labor you can find expects higher wages and more benefits. Labor costs are up over 8% in many markets. This represents the largest increase in 20 years and can be expected to continue. From my perspective, it is a great time to be a supply chain consultant as everyone is trying to find the Secret Sauce to achieving supply chain success. While I don’t believe the answer exists in one single solution, there are many opportunities available to meet the challenge.
These include:
- Network optimization
- Automation
- Financial and Labor Management
This blog will address Network Optimization, while subsequent blogs will address Automation and Financial and Labor Management.
Network Optimization
More than ever, our clients are taking a step back to critically evaluate their overall supply chains. They are certainly concerned with having the right inventory in the right place at the right time. However, issues such as backlogs in the ports, a ship blocking the Panama Canal, truck driver shortages and COVID make this a moving target to try and plan for.
Evaluating your supply chain is more than determining how many and where your distribution facilities need to be located in the United States. It needs to include an evaluation of whether inventory for the next season should be offshore, near shore (such as Mexico) or on shore to ensure availability and provide high levels of customer service. This includes evaluating the ports you utilize, understanding the risks associated with Mexico and the variability of the benefits of De Minimus savings, along with other considerations.
Developing the best plan is no longer a single answer but a series of options that requires sensitivity analysis to ensure the highest probability of achieving an agile supply chain.
Should I use in-house or outside modeling support?
There are 3 options to consider in determining who should do the modeling:
- In-house
- Outsource
- Hybrid of outsourcing while developing an in-house capability
If your intention is to establish network modeling as a core competency to be utilized on a regular basis, then developing in-house capabilities makes sense.
It the expectation is to model every 3-5 years, then outsourcing is best.
In the hybrid option, your organization can choose a consulting partner to work with on the initial model while including an in-house resource to work with the consultant to gain the experience required. This option provides you with the greatest flexibility.
Modeling Overview
As with any supply chain initiative, you need to establish the baseline of where your network is today in order to identify potential areas for improvement. The process starts with documenting the flows of merchandise from the source to the end customer and should, where applicable, include any reverse logistics flows as well. These flow lanes and their associated volumes and negotiated freight rates will allow the network to be modeled. There are many network modeling programs available to perform the analysis. Examples are Llamasoft, Insight Supply Chain Optimizer and AIMMS. These tools include graphics to show the flows along with the supporting data including cost and service-level capabilities.
The graphic below provides an overview of the modeling process.
The baseline costs developed from the model should be within 5-10% of the actual cost to provide a reasonable base against which to compare options. The next step is to input the future growth projections into the model. With the future baseline established, multiple iterations of options are easily run. While it is typical to run 5-10 options, it is likely that these will evolve into more runs as ”WHAT IF?” questions arise, such as WHAT IF… sales exceed projections, a port is shut down, a location is out of commission due to a natural disaster? The list is endless.
Conclusion
Once options have been developed and fully vetted, it is time to begin moving from strategic planning to tactical implementation. There are numerous options to consider for optimizing operations; however, lead times on many are 12-24 months. In the subsequent blogs in this series, we will explore options that can be implemented in less than 6 months as well as longer term options. You will need to consider all these options to keep your supply chain FLEXIBLE, SCALABLE AND AGILE.
It is safe to say that today’s supply chain issues are both a blessing and a curse. We are definitely living in INTERESTING TIMES. We have no choice but to rise to the challenge.
If you would like to explore this topic further, please reach out to us. We will also be presenting these topics and more during our Virtual Conference, Supply Chain Agility 2022, on March 15th and 16th. We look forward to having you attend. An invitation is coming soon!